Tank Welding Inspection: Guaranteeing Long-Term Durability and Security
Tank Welding Inspection: Guaranteeing Long-Term Durability and Security
Blog Article

Comprehending the Significance of Rigorous Storage Tank Welding Assessment Processes in Fighting Failings and Enhancing Lifespan
In the realm of commercial procedures, the value of extensive storage tank welding inspection processes can not be overemphasized. By carrying out numerous examination methodologies, organizations can find flaws early, thereby preventing pricey repercussions and extending the life of their storage containers.
Relevance of Welding Assessments
Recognizing the important function of welding inspections in maintaining architectural honesty, these processes guarantee that welds satisfy recognized standards and specs - Tank Welding Inspection. Efficient welding examinations are paramount in the building and construction and upkeep of tanks, as they directly impact the resilience and security of the structures. By identifying possible deficiencies, such as improper techniques or product flaws, inspections alleviate the risk of tragic failings
Welding evaluations encompass various approaches, consisting of aesthetic examinations, non-destructive screening (NDT), and assessments of welding procedures. Each method offers to confirm the high quality and conformity of welds with market guidelines, consequently protecting both workers and environmental interests. Normal assessments promote a culture of responsibility and quality within the workforce, guaranteeing that all group participants adhere to ideal practices.
Moreover, these inspections add to the general lifecycle monitoring of storage tanks by identifying wear or deterioration early in the process. By addressing these problems proactively, companies can expand the operational lifespan of their possessions, inevitably resulting in cost financial savings and boosted reliability. In summary, the relevance of welding assessments can not be overemphasized; they are necessary for ensuring security, durability, and conformity in tank building and upkeep.
Usual Reasons of Container Failings
Recognizing the usual reasons of container failures is important for protecting against disastrous incidents and making sure the longevity of storage systems. One common root cause of container failing is deterioration, which can substantially deteriorate the structural integrity of tanks gradually. Environmental aspects, such as direct exposure to moisture, chemicals, and temperature level fluctuations, can increase this procedure.
Another critical variable is incorrect welding methods, which may bring about flaws like cracks or incomplete joints. These problems can jeopardize the storage tank's stamina and cause leaks or tears. Additionally, inadequate maintenance techniques can lead to undiscovered damage, eventually enhancing the danger of failing.
Layout problems, including inadequate density or poor material selection, can additionally contribute to container vulnerabilities. Operational aspects, such as overfilling or exposure to severe stress, can strain the container beyond its desired limits.
Trick Evaluation Techniques
Efficient inspection methods play a vital function in minimizing the risks related to container failings. A detailed method to container welding evaluation entails several crucial additional hints strategies, each developed to determine possible problems and make sure structural integrity.
Aesthetic assessment stays the very first line of protection, permitting inspectors to determine surface abnormalities such as splits, deterioration, or see this here imbalance. This strategy is typically supplemented by non-destructive screening (NDT) methods, which are important for examining weld top quality without jeopardizing the tank's integrity.
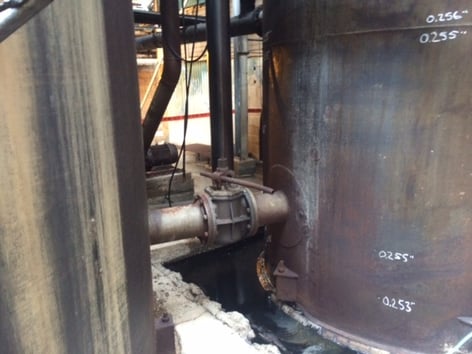
Moreover, magnetic particle testing (MPT) and dye penetrant testing (DPT) work for identifying surface problems in ferromagnetic materials and non-porous surfaces, respectively. Each method has its staminas and constraints; consequently, a mix of methods is often employed to achieve extensive assessment outcomes.
Advantages of Strenuous Inspections
While the immediate costs of rigorous inspections may appear daunting, the long-term advantages dramatically surpass these first financial investments. Applying complete examination refines not just boosts the stability and safety of tank structures yet additionally lessens the danger of devastating failures that can result in significant economic losses and ecological injury.
Strenuous evaluations aid identify possible problems early in the welding procedure, enabling timely corrective activities that prevent costly fixings or replacements down the line. This proactive approach cultivates a society of quality control, where adherence to ideal methods becomes implanted in functional procedures. Routine assessments add to enhanced asset long life, as they ensure that storage tanks remain in ideal condition throughout their life expectancy.
In addition, the documentation created from these examinations works as a beneficial resource for maintenance preparation and performance assessments. This data-driven approach can additionally boost functional performance, bring about decreased downtime and boosted efficiency. Eventually, extensive assessments not just protect the architectural stability of containers however likewise give significant financial advantages, reinforcing the concept that purchasing quality control is a wise choice for any company entailed in container procedures.
Regulatory Standards and Conformity
Regulative requirements and conformity are vital components of container welding inspection procedures, as they develop the structure for making certain safety and security and high quality in procedures. Compliance with these requirements not just visit our website minimizes dangers but also boosts the overall honesty of welded frameworks. Different companies, consisting of the American Society of Mechanical Engineers (ASME) and the American Oil Institute (API), give standards that determine acceptable methods for welding, examination, and testing.
These requirements mandate using qualified personnel, the execution of extensive evaluation methods, and adherence to details welding treatments. By lining up with regulative needs, companies can make sure that their tanks satisfy the needed safety and performance criteria, thus reducing the chance of tragic failures that can result in substantial monetary losses and ecological damages.

Additionally, regulative compliance promotes a culture of responsibility and continuous renovation within the welding and manufacture fields (Tank Welding Inspection). Regular audits and examinations make certain that techniques remain straightened with progressing standards, therefore advertising long-term integrity and operational performance. Eventually, adherence to regulatory standards not just protects properties however also boosts the lifespan of welded tanks, guaranteeing they serve their desired purpose efficiently over time
Verdict
In final thought, rigorous container welding evaluation processes play a vital duty in protecting against failings and extending the lifespan of storage space structures. By determining prospective deficiencies through various inspection methods, companies can minimize threats connected with container integrity.
Report this page